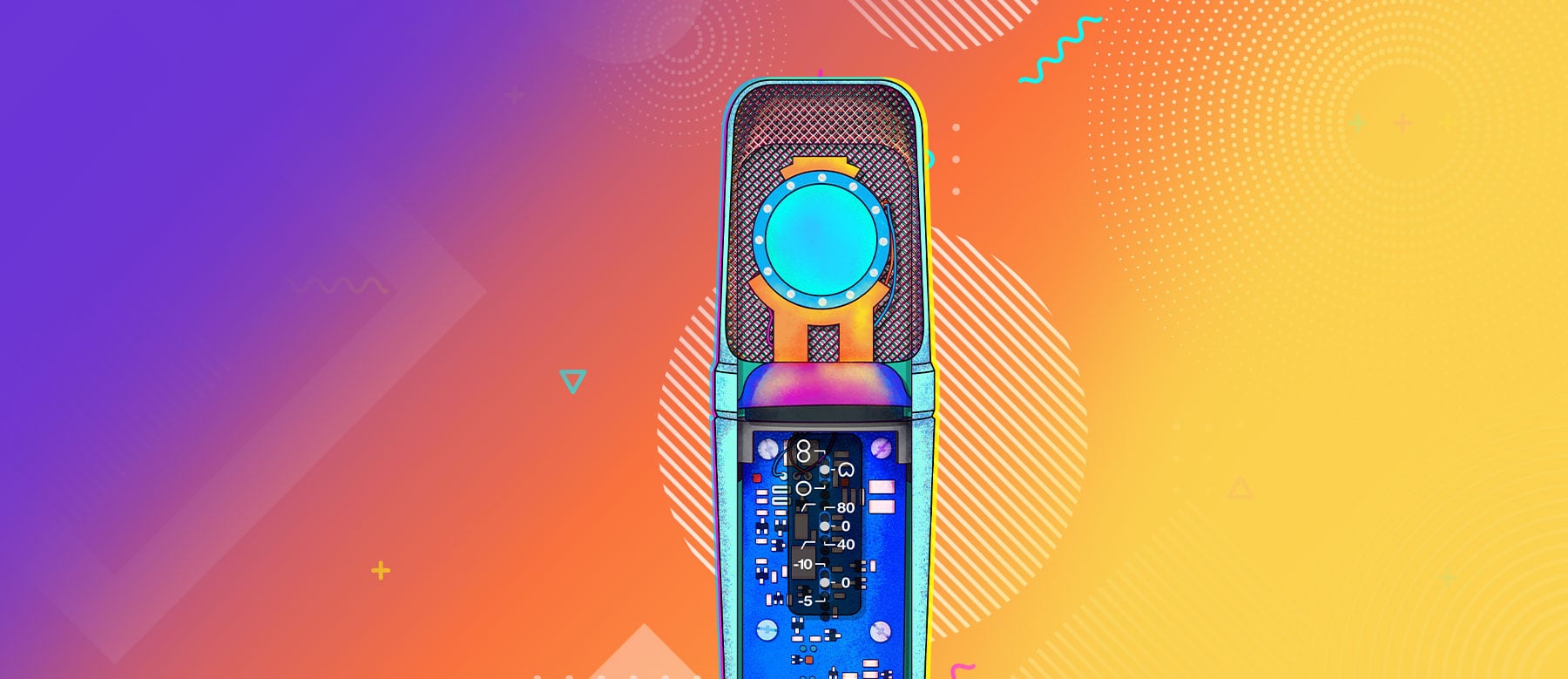
Condenser Microphones
In the fourth instalment of this series, Greg Simmons delves deep into condenser microphones...
In the previous two instalments we looked at how ribbon and dynamic microphones work, why they sound the way they do, when to use them and when to avoid them. This time we’re looking at condenser microphones: how they work, how their design has changed in response to new technologies, the factors that influence their characteristic tonality and, of course, when to use them and when to avoid them.
CONDENSER MICROPHONES
The condenser microphone was invented at Western Electric in 1916 by Edward Wente. (Fifteen years later he Wente and did it again, teaming up with Albert Thuras to invent the practical dynamic microphone as discussed in the previous instalment.) Early condenser microphones were dull and noisy, and were quickly replaced by ribbon microphones in the 1930s. Improvements in condenser microphone technology brought them back into vogue in the 1960s.
It’s worth noting that in the early days of electronics the word ‘condenser’ referred to an electronic component called a capacitor that provided capacitance, which is fundamental to how condenser microphones convert sounds into signals. The old term condenser has stuck for the microphone design, although some manufacturers use the contemporary term capacitor microphone.
CONDENSER TRANSDUCTION
Unlike ribbon and dynamic microphones, condenser microphones do not use the principle of magnetic induction; instead, they manipulate (or modulate) an electrostatic charge. To understand how this works we must first understand the concept of capacitance, which is the ability to store an electrostatic charge.
A capacitor is an electronic component designed to provide capacitance. It consists of two parallel conducting surfaces, or plates, with an insulating material called a dielectric between them. Because it is an insulator, the dielectric prevents any direct electrical connection between the plates.
The electrostatic charge is stored between the plates; the amount of charge is determined by three things: the surface area of the plates, the distance between the plates, and the amount of voltage applied across them. When a voltage is applied, an electrical current flows until the capacitor is fully charged. Once the capacitor is fully charged, no more electrical current will flow unless something causes the amount of charge to change – for example, changing the distance between the plates. This is the key to understanding how the condenser microphone works.
Like the dynamic microphone, the condenser microphone uses a diaphragm to sense the vibrating air molecules caused by sound. Unlike the dynamic microphone, the condenser microphone’s diaphragm is designed to be one plate of a capacitor. It’s usually made of a strong and lightweight plastic material with a gold sputtering on one side to make it conductive. Gold is a good choice for this application because it does not corrode under normal atmospheric conditions (which is also why a gold plating is often found on electrical connections, even though copper is a superior conductor.) The sputtering is extremely thin and the end result is often translucent, like gold-coloured cellophane. Some manufacturers use a conducting foil made of aluminium, titanium or nickel, but these materials are less common.
The diaphragm is placed in parallel with – but not touching – a conducting surface of the same shape and area, usually machined from brass and known as the backplate. The diaphragm and backplate form a capacitor, with the air in the gap between them as the dielectric. Applying a voltage difference across the diaphragm and backplate will cause current to flow until the capacitor is fully charged – which is the condenser microphone’s starting point for converting sounds into signals.
Sound vibrations cause the diaphragm to vibrate. With each cycle of vibration, the distance between the diaphragm and backplate gets momentarily larger and smaller before returning to normal, varying the amount of charge that can be stored and thereby causing electrical current to flow one way or the other as the capacitor charges and discharges. The electrical current flow is proportional to the sound vibrations that move the diaphragm, and can be considered as a signal.
The capacitor created by the diaphragm and backplate has a very high output impedance and the signal created by it has very low power, so a buffer amplifier inside the microphone converts it into a useful output signal. In contemporary designs this buffer amplifier is usually based around a Field Effect Transistor (FET); in tube microphones it is a tube, of course. In both cases, the buffer amplifier needs a high input impedance so it does not take much power from the capacitor itself, and a low output impedance with a balanced differential output suitable to send a signal down a mic cable and into a preamp. Because the buffer amplifier takes the very high impedance from the capacitor and converts it into a low impedance output, microphone designers often refer to it as an impedance converter rather than a preamplifier – which conveniently avoids confusion with the term preamp that is commonly used to refer to an external microphone preamplifier.
Unlike passive ribbon and dynamic microphones, which generate their own signal, the condenser microphone needs a source of electrical power to operate; it needs a voltage source to provide the current to charge the capacitor, and it needs to power the impedance converter circuit. The electrical power is usually provided via +48V phantom power, but could also be from an internal battery as seen in early Neumann U87s, or from an external power supply as used for tube microphones and high voltage condensers.
Condenser microphones come in many different shapes, sizes and specialities – rather like domestic dog breeds. They are available in every known polar response, with many offering multiple polar responses through interchangeable capsules or the clever electronics found in dual-diaphragm designs. Some – such as Schoeps’ MK5, Shure’s KSM141 and Josephson’s C715 – use mechanical shutters to change polar responses between cardioid and omnidirectional.
FACTORS AFFECTING TONALITY
Condenser microphones commonly used for professional audio come with diaphragms varying in diameter from under 5mm to over 25mm. The diaphragm’s diameter affects the performance in numerous ways. From a tonality point of view, however, the most significant affects are on the high frequency performance and the self-noise.
DIAPHRAGM DIAMETER
The high frequency limit of a condenser microphone with a circular diaphragm is primarily determined by the relationship between its diameter and the wavelength of the frequency being captured. At frequencies where the wavelength is considerably larger than the diameter, the diaphragm is too small to have any affect on the tonality of the captured sound. At frequencies where the wavelength is considerably smaller than the diameter, the diaphragm is big enough to be an obstacle and therefore have a significant affect on the tonality of the captured sound. And at frequencies where the wavelength is the same size as the diameter, a situation can occur where the diaphragm is receiving equal amounts of energy from both halves of the waveform (positive and negative), which cancel each other out and create a null (i.e. zero output). This frequency – where the wavelength is equal to the diameter of the diaphragm – theoretically determines the upper limit of a condenser microphone’s frequency response because it defines the first null point, but it’s not that straightforward…
Unlike the simple maths for determining a ribbon microphone’s high frequency limit [as shown in the second instalment], the high frequency limit of the condenser diaphragm is also affected by the angle of incidence and the way the diaphragm is mounted. For any given diaphragm, the high frequency limitations will be different in a side-address configuration than in an end-address configuration, and different again if mounted in a diffraction sphere or fitted with an equalising ring or diffusion grid.
It gets complicated when trying to define the upper frequency limit of a condenser microphone with a simple formula or rule. It is, however, worthwhile putting the concept of ‘wavelength’ into perspective with diaphragm diameter. The range of human hearing is considered to exist between 20Hz and 20kHz. Assuming a room temperature of 21°C, 20Hz has a wavelength of 17.2m – that’s how long one cycle is in the air. It’s significantly bigger than any practical microphone. At 20kHz, however, the wavelength is only 17.2mm long. It’s significantly smaller than the 25mm diaphragms commonly seen in dual-diaphragm microphones and is therefore affected by them.
Based on this knowledge, we’ll use 17mm (close enough to the wavelength of 20kHz) as a threshold point for differentiating between small and large diaphragms. There are no hard-and-fast rules for this, but condenser microphones with diaphragm diameters less than 17mm are generally described as SDCs (Small Diaphragm Condensers) while microphones with diaphragms of 20mm or more are generally described as LDCs (Large Diaphragm Condensers). Condenser microphones with diaphragm diameters less than 17mm usually exhibit extended high frequency response and better off-axis response when compared to those with diaphragms larger than 17mm.
Due to the very light weight of the diaphragm and the potential to make it very small, it is not difficult to make a condenser microphone with a frequency response extending up to 20kHz – the upper limit of human hearing. Maintaining a consistent response beyond 20kHz becomes more of a challenge, but is important for those who need to record sounds with content above the range of human hearing; whether to slow it down to create sound effects for movies and games, pitch-shift it down to analyze bat calls and insect sounds, or make ‘high resolution’ recordings for the audiophile market.
Condenser microphones come in many different shapes, sizes and specialities – rather like domestic dog breeds.
OFF-AXIS RESPONSE & TRANSIENTS
A sound arriving from directly in front of the microphone, perpendicular to the diaphragm, is considered to be on-axis, and is said to be arriving at the diaphragm from an angle of 0°. For the purpose of this discussion any sound arriving from an angle other than 0° can be considered to be off-axis because it is no longer coming directly on-axis. (This is discussed in a later instalment where we look at microphones’ polar responses and acceptance angles.)
As the diaphragm gets larger it becomes more directional at higher frequencies. As a result, sounds arriving significantly off-axis will be duller than sounds arriving on-axis. This is generally referred to as a poor off-axis response and results in a reduction of overall high frequency energy relative to low frequency energy captured by the diaphragm. Poor off-axis response at high frequencies is a characteristic of all large diaphragm mics and fuels the myth that large diaphragms have better low frequency performance than small diaphragms, when the reality is that they have worse high frequency performance (as discussed in the previous instalment, see ‘Subkick microphones’).
As the diaphragm gets smaller its off-axis response improves. This is one of the reasons why small diaphragm condensers are often preferred for main stereo pairs when making distant-miked recordings of orchestras, choirs, pipe organs and chamber music – all situations where sounds arriving from all directions (including early reflections, reverberation and audience reaction) need to be captured with a consistent tonality. If not, the sounds arriving off-axis will be duller than those arriving on-axis and result in a sound that could be described as ‘muddy’ or ‘roomy’.
A microphone’s off-axis response is not much of an issue when close-miking a single instrument, but it can be an issue if you are close-miking a number of instruments playing together in the same space. After doing what you can to minimise spill by the strategic use of instrument placement, baffles and polar response rejection (as explained in later instalments), you’ll want the remaining spill to be captured clearly so it doesn’t muddy up the sound when all the mics are blended together in the mix. The better off-axis response of smaller diaphragms can have a cumulatively positive effect in this situation.
As a generalisation, the large diaphragm condenser’s reduced high frequency capture and accompanying slower transient response means it tends to sound mellower and potentially smoother than a small diameter condenser, but with inferior off-axis response. Regardless of the diameter, however, the condenser microphone’s diaphragm is always going to be significantly lighter than a similarly-sized dynamic microphone’s diaphragm/coil assembly and can therefore move much faster, giving it excellent high frequency performance and transient response in comparison.
EQUIVALENT NOISE LEVEL
In ribbon and dynamic microphones the primary source of noise is thermal noise, as explained in the previous two instalments of this series (1) (2). This form of noise is rarely mentioned in their specifications because it is very low and will be insignificant compared to the noise from the preamplifiers they are connected to – which tend to be used at higher gains than they would be with condensers due to the lower outputs of ribbons and dynamics.
In condenser microphones the term equivalent noise level usually refers to the combination of the diaphragm’s self-noise and the noise from the microphone’s electronic circuitry. Self-noise refers to noise caused by air particles randomly striking the surface of the diaphragm. This form of noise is not a problem with dynamic microphones because their considerably heavier diaphragms are less sensitive to the random impacts of air molecules. It’s also not a problem with ribbon microphones because their ribbon elements are not held under enough tension to make them sufficiently responsive to random impacts of air molecules.
Self-noise and equivalent noise level are explained in detail in the following instalment of this series. For now, the important thing to know is that with all other parameters being equal, a large diaphragm will have less self-noise than a small diaphragm. It will also have greater sensitivity than the small diaphragm (meaning it provides a higher output level from the same sound source) but with a lower maximum SPL. So if you need to make a very quiet recording or if you need to record something that has very low volume, a large diaphragm condenser is a better choice than a small diaphragm condenser; it is quieter due to its lower self-noise, and its higher sensitivity requires less preamp gain and associated noise. If you need to record something very loud, a small diaphragm is a better choice; it can handle higher SPLs with ease, its lower sensitivity means less chance of overloading your preamp, and its higher self-noise won’t be an issue with a loud sound source. There’s more discussion about this kind of decision making in a later instalment of this series…
The noise from the electronic circuitry inside the microphone also needs to be considered. All active electronic circuits create noise – especially when that circuit has to work with the very small signals coming from a microphone capsule. (For many years this form of noise was unique to condenser microphones, but nowadays it also exists with active ribbon mics, active dynamic mics, USB mics and any other mic that has electronic circuitry in it.)
A presentation by Neumann’s Martin Schneider compared the frequency spectrum and amplitude of the diaphragm’s self-noise and the internal electronics’ noise for a large diaphragm condenser with a very low equivalent noise level. When averaged across the audible spectrum from 20Hz to 20kHz, the noise from the microphone’s internal electronics was approximately 3dB lower than the diaphragm’s self-noise. The large diaphragm microphone used in this example has an equivalent noise level of only 7dBA, therefore the noise from the microphone’s internal electronics (being on average just 3dB lower than the diaphragm’s self-noise) could be considered significant. Microphones with very small diaphragms (i.e. 6mm or less), such as Earthworks’ QTC30 or DPA’s 4060, have equivalent noise levels of 20dBA or more, most of which is self-noise. In these examples the noise of the microphone’s internal electronics is probably insignificant.
RESONANCE
Because the diaphragm is usually a circular membrane held under tension, it behaves like a tiny drum (imagine a miniature roto tom) with a strong primary resonant frequency, or note, of its own. Any sound that contains frequencies at or near the diaphragm’s resonant frequency will cause the diaphragm to resonate, emphasizing those particular frequencies above others and thereby adding to the microphone’s characteristic tonality.
The condenser microphone designer tweaks the diaphragm’s diameter, mass and tension to determine its resonant frequency – which typically ends up somewhere between 5kHz and 9kHz – and then decides how much damping should be applied to control the resonance. Increasing the damping reduces the strength of the resonance (which is equivalent to lowering the amount of boost on a peak/dip equaliser), but also reduces the diaphragm’s overall sensitivity (which is like lowering the fader). There is always a compromise between resonance and sensitivity, hence the market is full of condenser microphones with a characteristic boost in the upper midrange or high frequencies – often engineered and marketed as a feature to provide enhanced detail or to compensate for the loss of high frequencies through the air when distant miking. This balance of resonance and damping is another factor that determines how the condenser mic affects the tonality of the captured sound.
Most condenser diaphragms are ‘edge terminated’ which means the electrical connections (or ‘terminations’) to the diaphragm and backplate are made at the edges, leaving the diaphragm free to move. Some are ‘centre terminated’, which means the electrical connection is made to a terminal in the centre of the diaphragm – as seen in Neumann’s classic U47 and U67 mics respectively. This is like lightly placing your finger in the centre of a drum skin and listening to how it affects the resonances and therefore the tonality; it changes the balance of the diaphragm’s resonant modes, but in the case of the U47 and U67 it’s just one of many things that affect or determine their tonality. Another is, of course, their tube circuitry…
INTERNAL ELECTRONICS
Every circuit that an audio signal passes through imparts its own sonic fingerprint on that signal (typically as a combination of its inherent harmonic and intermodulation distortions), and every condenser microphone includes an impedance converter circuit that the signal must pass through in the process of becoming useable. That circuit will contain numerous electronic components, but the primary component will be an amplifying device of some kind (tube, FET, transistor, etc.) that imparts its own sonic fingerprint, contributing to the microphone’s overall tonality.
As with ribbon and dynamic mics, for many years a transformer was used to give the condenser microphone a balanced differential output suitable for sending a signal down a microphone cable and into a preamp. Contemporary designs use a solid state electronic circuit and don’t require an output transformer, although many still use one. The acronym ‘TLM’, used in the model names for many of Neumann’s contemporary microphones, stands for ‘Transformer Less Microphone’. Similarly, when DPA made an updated version of their classic 4006, ‘TL’ was appended to the model number to indicate it was ‘Transformer Less’. According to DPA’s documentation, removing the transformer allowed the 4006TL’s low frequency response to be extended downwards another octave from 20Hz to 10Hz.
Some condenser microphone manufacturers have returned to using transformers primarily for their ‘old school’ tonal properties, or simply to take advantage of the transformer’s relative simplicity for providing a balanced differential output. When Audio-Technica designed the 5047 – a premium version of their 5040 – they added a transformer output to maintain a ‘constant load output impedance’ and provide a ‘smooth sonic character’. [The effect of a varying load impedance was discussed in the second instalment of this series; it is the reason why the tonality of a passive ribbon microphone can be affected by the preamp it is connected to.]
BACKPLATE
Another factor that affects the tonality of a condenser microphone is the profiling and perforations of the backplate which, among other things, affect how the microphone responds to sounds arriving from off-axis. Traditionally hand-profiled by skilled craftspeople working with tiny files, screw gauges and magnifying glasses, it’s one of the reasons why condenser microphones with good off-axis responses used to cost so much. Contemporary computer-controlled machining is now able to achieve very high tolerances, reducing manufacturing time and costs.
The diaphragm material also contributes to the tonality of a condenser microphone. Diaphragms are commonly made of a light but strong plastic material such as Mylar, but other materials include nickel, titanium, aluminium and stainless steel. The inherent resonances and vibrational modes of these materials will each add their own tonality to the sound they produce, in the same way that different drum skin materials will sound different on the same drum, and in the same way that steel strings sound different to nylon strings when fitted on the same guitar. Unlike the ribbon microphone, the condenser microphone’s diaphragm is held under considerable tension and has a high resonant frequency and, unlike the dynamic microphone, there is no coil to provide mass damping to the diaphragm’s natural behavior. However, as discussed in a later instalment of this series, the condenser microphone’s diaphragm is so light that the air itself provides some damping.
ADVANCES
Considering that the condenser microphone design dates back to 1916 it should come as no surprise that there have been significant advances based on new technologies since then, along with ideas borrowed from ribbon and dynamic microphone developments, and new ideas specifically related to how the condenser transducer works. Let’s look at some of them…
TUBES & FETS
Early condenser microphones used tube circuits in their impedance converters. Although tubes were the only options for amplification at the time, their very high input impedances made them an ideal match for the high output impedance of the condenser capsule. However, in addition to being relatively large electronic devices, tubes require high voltages to operate (typically measured in hundreds of volts), which in turn require the use of high voltage internal components, the need for heat dissipation, and the use of external power supplies. The arrival of the considerably smaller and low-powered Bipolar Junction Transistor (BJT) offered great potential for microphone designers, but its low input impedance made it difficult for working with condenser capsules – a problem that ultimately motivated investigations into RF designs, as discussed below. The commercial availability of the Field Effect Transistor (FET) in the 1960s, with its very high input impedance, fulfilled the promise of the transistor and allowed physically smaller and lower-powered condenser microphones to be made; ultimately paving the way for phantom powered microphones.
Comparing Neumann’s U47 tube microphone from 1949 to their phantom-powered U47FET from 1969 shows a considerable saving in size, weight and set-up time. Despite using the same K47 capsule, the two microphones sound different due to the electronics used in their impedance converter circuits. Every electronic circuit introduces its own distortions: some pleasantly harmonic, some unmusical and dissonant. The distortion components of tube circuits are generally considered to be more ‘musical’ than those of transistor circuits, which goes a long way towards explaining not only the tonal differences between the U47 and U47FET, but between tube circuits and transistor circuits in general. It’s also worth noting that the U47FET uses a significantly different output transformer than the original U47, another factor in the differing tonalities.
Although tubes are capable of very low-distortion performance, the circuits used in some contemporary tube microphones (and other audio devices) are sometimes intentionally designed to exaggerate the more musical aspects of the tube’s inherent distortions – resulting in microphones that sound lovely and warm on first listen, but repeated use unveils a strong sonic fingerprint and tonality that dominates every sound that passes through them. Too much of a good thing…
Audio-Technica had the balance right with their AT3060; a large diaphragm cardioid condenser microphone that sounded particularly good on vocals and narration. Discontinued long ago, the AT3060 was unique among tube mics in that it was phantom powered; it used a miniaturised low power tube originally designed for use in hearing aids, bypassing the need for an external high voltage power supply and the associated set-up time. It plugged directly into the preamp with a standard microphone cable.
It’s all explained with science and physics, of course, and the only ‘magic’ should be the impression left in the listener’s ear.
DUAL DIAPHRAGMS
No discussion of condenser microphones would be complete without mentioning the dual-diaphragm design that allows varying polar responses. Invented by Von Braunmuhl and Weber in the 1930s, the design uses two back-to-back cardioid capsules that can be combined to create every first-order polar response from omni to bidirectional. [How this works is discussed in a following instalment of this series.] The first commercially available microphone to use this dual-diaphragm approach was Neumann’s U47, released in the late 1940s and using Neumann’s M7 capsule (later replaced with the K47 capsule). The U47 offered switchable cardioid and omni polar responses, while the U48, released some time later and also initially using the M7 capsule, offered switchable cardioid and bidirectional polar responses. Since then, dual-diaphragm condenser microphones have become a mainstay of every microphone collection, and are commonly used for recording vocals.
In most cases the polar responses are selected by switches on the body of the microphone, with typical options being omni, cardioid and bidirectional – although some also offer hypercardioid and subcardioid. Røde’s versatile NT2000 uses a rotary potentiometer to provide a continuously variable polar response (along with continuously variable pad and high pass filter) allowing it to be fine-tuned in-situ, an invaluable feature for rejecting spill when used for spot-miking in large ensembles. Neumann’s classic M49, dating back to the early 1950s and discontinued in the early 1970s, was the first mic to offer continuously variable polar responses, and did it from the power supply rather than the mic itself, which allowed an element of remote control. Lewitt, Josephson, Pearl and Sennheiser, among others, offer dual-diaphragm microphones with separate outputs for each diaphragm, allowing the user to fine-tune the polar response in real-time during monitoring. By recording the outputs of the separate diaphragms onto individual tracks, the polar response can be fine-tuned after the recording – polar response changes can even be automated during the mix.
In the late 1990s Guy Torio and Jeff Segota of Shure presented an excellent paper revealing a number of differences between single-diaphragm and dual-diaphragm condensers, comparing mathematical models with actual devices to confirm their results. One valuable takeaway is that, with all other parameters being equal, the dual-diaphragm has less proximity effect and less ‘popping’ on plosives than the single-diaphragm. This reinforces the popular choice of dual-diaphragm microphones for close-miking vocals; the lower proximity effect makes the dual-diaphragm more forgiving to changes in distance, and less susceptible to plosives.
FOUR OR MORE…
Ambisonic microphones such as Sennheiser’s AMBEO VR and Røde’s NT-SF1 use four coincident diaphragms, allowing any polar response from omni to bidirectional to be created while also allowing that polar response to be steered to face any direction. Multiple polar responses, each facing different directions, can be extracted from the same four diaphragms to create a coincident stereo or multichannel microphone. Core Sound’s Octomic takes the concept even further, using eight diaphragms. [Ambisonic microphones are discussed in a later instalment of this series…]
SPHERES & GRIDS
Neumann’s classic M50, released in 1951, showed a different way to create a useful polar response. By flush mounting a 12mm omnidirectional diaphragm on a 40mm sphere they created a microphone that was omnidirectional at low frequencies but became increasingly directional at higher frequencies. Along with the increased high frequency directivity, the sphere brought with it a high frequency shelf that departed from 0dB at around 1.8kHz and rose to +5dB at 3kHz, from where it leveled out. So although the microphone’s polar response captured a narrower area of high frequency energy compared to low frequency energy, the high frequency boost compensated for this and also for the loss of high frequencies in the air over distance, producing a microphone that did not sound as dull as the narrowing polar responses suggested, but did not sound as bright as the on-axis frequency response suggested. By aiming the M50’s axis appropriately, distant instruments within a large ensemble could be captured with similar tonality, clarity and presence as close instruments – making it a favourite for recording orchestras and similar large ensembles. Despite being a small single-diaphragm condenser, the M50’s tonality and physical size (it uses the same housing as the M49) means it is often assumed to be a large dual-diaphragm condenser.
DPA took Neumann’s M50 idea one step further by creating a set of different diameter spheres and lozenges that could be fitted over their 4006 omnidirectional microphone – including a 40mm sphere to create similar characteristics as the M50. Packaged together as the ‘Acoustic Pressure Equaliser’ (APE) kit, the latest version dispenses with the lozenge-shaped options and provides three spheres at 30mm, 40mm and 50mm diameter. DPA also make a set of interchangeable screw-on grids for the front of the 4006 – optimising its frequency response and polar response for use in free field, diffuse field and close-miking situations – along with a screw-on nosecone to provide an improved omnidirectional polar response. Their 4015 wide cardioid and 4041 omnidirectional both use cleverly designed diffraction grids on the front to provide a high frequency boost on axis, allowing them to be used at greater distances without sacrificing detail due to absorption of high frequencies in the air.
NON-CIRCULAR DIAPHRAGMS
One interesting solution to the circular diaphragm’s strong resonance discussed earlier is to avoid using a circular diaphragm. Pearl and Milab (now merged into one company) have both been making rectangular-shaped diaphragms for decades, and, more recently, Audio-Technica have adopted rectangular diaphragms for their 5000 series of high end condenser microphones. A rectangular diaphragm replaces the circular diaphragm’s single strong fundamental resonance with two smaller and much weaker fundamental resonances – one for the length, and one for the width – which are both much easier to control. Ehrlund is offering microphones with triangular-shaped diaphragms for similar reasons. Reviewers consistently use words like ‘natural’, ‘smooth’ and ‘pure’ to describe the tonality of microphones that use non-circular diaphragms.
That doesn’t mean a condenser will always be the best choice, but it will usually be an acceptable choice.
MULTIPLE CAPSULES
Among the on-going challenges faced by condenser microphone designers are the trade-offs between diaphragm size and performance, as discussed earlier in this instalment. Larger diaphragms are quieter and more sensitive than smaller diaphragms, but at the expense of poorer off-axis response, slower transient response and lower SPL handling. In an attempt to get the best of both worlds, some manufacturers combine multiple small diaphragms together in the same microphone to provide the high frequency performance, transient response and SPL handling of a smaller diaphragm with the lower self-noise and greater sensitivity of a large diaphragm.
Audio-Technica combine four rectangular diaphragms in their 5040 and 5047 microphones to combine the low noise benefits of a large diaphragm with the speed and detail of a small diaphragm. DPA take a similar approach with their 2006 and 2011 microphones, which both use ‘Twin Diaphragm’ capsules that combine a pair of DPA’s tiny 4060-style diaphragms into one capsule. Similarly, Line Audio developed their ‘triple membrane capsule’, combining three small diaphragm capsules into one microphone to create what they described as a “large membrane area using triple small membranes”. It was used in their SM, ST and QM series of studio microphones.
Sanken have been making dual capsule condenser microphones since 1982. Their CU-41, CU-51 and CU-44X MkII all use two capsules, one above the other, for faster transient response and extended high frequency response.
BEYOND 20KHZ
While the big challenge for dynamic and ribbon microphone designers is getting useful response up to 20kHz, some condenser microphone designers have responded to the use of high sampling rates by making microphones with bandwidths up to and exceeding 50kHz. Sennheiser’s MKH800 dual-diaphragm microphone and their MKH8000 series of single-diaphragm condensers all offer bandwidths up to 50kHz, as does Sony’s ECM-100U, ECM-100N and C-100. The latter is particularly interesting because it’s a two-way design that Sony describes as ‘invented for vocals’. It combines a large diaphragm capsule – always popular for vocal recording – with a small diaphragm electret condenser placed immediately above it to push the bandwidth up to 50kHz. Meanwhile, Sanken take it up another octave with their omnidirectional CO-100k which, as the name implies, extends the bandwidth to 100kHz.
RF CONDENSERS
With the exception of electrets (discussed below), all of the condenser microphones mentioned so far require a DC voltage to charge the condenser. As explained earlier, they use the changing capacitance created between the vibrating diaphragm and the backplate to vary, or modulate, an electrical current that ultimately becomes the signal.
Instead of modulating an electrical current, the varying capacitance created between the backplate and the vibrating diaphragm can be used to modulate the amplitude or the frequency of a very high frequency oscillator, relying on the principle of Amplitude Modulation (AM) or Frequency Modulation (FM) to demodulate and extract the audio signal. The high frequency oscillator is typically tuned to a frequency measured in MHz and therefore considered to be in the bandwidth of radio frequencies, otherwise known as ‘RF’. Microphones that use this approach are therefore called ‘RF condensers’.
The RF approach offers numerous advantages over the traditional (DC) approach, but also presents a number of design challenges. Many manufacturers experimented with RF techniques in the early days of solid state condenser microphones – primarily as a way of working around the relatively low input impedances of Bipolar Junction Transistors (BJTs) – but most found the associated design problems discouraging. Thankfully, Field Effect Transistors (FETs) arrived on the scene, bringing with them high impedance inputs and thereby removing the need to continue with RF designs.
Sennheiser persisted with the RF concept, however, resulting in their MKH series of small diaphragm microphones that feature low self-noise, extended frequency response, good off-axis response, and high immunity to humidity. These features have made them popular with sound engineers who record acoustic music (orchestral, chamber music, etc.) where low noise and good off-axis response is important, and also with location recordists, field recordists and others who need low noise and have to record outdoors – often in humid environments. Røde uses RF technology in their NTG3 and NTG8 shotgun microphones.
AES42 DIGITAL MICROPHONES
The concept of digital microphones has been around for many years. In the late 1990s the AES announced the AES42 standard which Neumann, Sennheiser, Schoeps and others supported.
The concept is simple: bring the preamp and converter into the microphone. In practice there is no need for a preamp because the capsule is connected directly to a gain-ranging AD converter that has a greater dynamic range than the diaphragm itself and is therefore able to convert everything the diaphragm is capable of producing, from self-noise to physical clipping – hence no need for an internal preamp. There are numerous advantages to this approach, with the obvious one being that it delivers the sound of the diaphragm itself without the added noise, colourations or distortions from the traditional condenser microphone’s impedance converter or from the external preamp it needs to be connected to.
The first AES42 mic on the market was Neumann’s Solution D-01, arriving in 2003 and spearheading their Solution D series that ultimately included AES42 versions of many of their most popular microphones. A recent announcement on Neumann’s website advises that the Solution D product line will be discontinued as of January 2021. Never reaching the widespread popularity that the concept deserves, it will be interesting to see how other AES42 manufacturers react to Neumann’s announcement.
ELECTRETS & MEMS
A very significant advance in condenser microphones came with the use of dielectric materials such as polytetrafluoroethylene (PTFE), that are capable of holding a permanent charge. These types of materials are known as ‘electrets’; a contraction of ‘electricity magnets’. They are not magnets, of course, but they can hold a permanent electrical charge in the same way that a magnet can hold a permanent magnetic charge.
A thin layer of electret material is applied to the backplate of the condenser microphone, giving it a permanent charge and removing the need for an applied charging voltage. For this reason, these microphones are commonly referred to as ‘electret’ or ‘back-electret’ microphones. They still require a voltage source to power the impedance converter circuit, but this can be provided by a simple battery or via Plug In Power (PIP).
Historically dismissed as sounding ‘harsh’, ‘brittle’ or ‘tinny’, with the right design and manufacturing processes they can sound excellent. Most, if not all, of DPA’s highly regarded condenser microphones are electrets, as are Shure’s Beta 181 series and their Beta 87A and Beta 87C handheld vocal mics. Most lavalier microphones (‘lavs’) are electrets. DPA wisely uses the term ‘pre-polarised condenser’ to avoid the stigma associated with the word ‘electret’. Similarly, the terms ‘externally polarised’ and ‘true condenser’ are often used to indicate that a microphone is not using an electret condenser.
One of the great advantages of electret microphones is that they can be made very small, very cheap, and can be powered with very low voltages; all factors that contribute to them being one the most commonly used microphones in the world. For many years you’d find electrets in every portable device that had built-in microphones (laptops, tablets, phones, cameras, handheld recorders, etc.). For many of these applications electrets have been replaced by MEMS (Micro Electro Mechanical System) microphones, which are miniaturised packages designed for surface-mounting directly on to a printed circuit board. The entire diaphragm and backplate assembly is fabricated on a silicon wafer, and the package often includes an internal analogue-to-digital converter to provide a digital output. Rather than using electret principles, MEMS microphones include a charge pump (i.e. a voltage multiplier circuit) to provide the charging voltage between the diaphragm and the backplate. They are finding rapid acceptance in portable devices due to their small size, surface mount capabilities and digital outputs. [MEMS show up throughout our mobile devices as microphones, speakers, accelerometers, gyroscopes, motion sensors and more. If it has moving parts and needs to be fitted into a mobile device, there’s probably a MEMS component to do it…]
APPLICATIONS & INDICATORS
The sheer diversity of options available from condenser microphones (large and small diaphragms, single and dual-diaphragms, every polar response, and a huge range of physical sizes) means there is a condenser microphone for just about any application. That doesn’t mean a condenser will always be the best choice, but it will usually be an acceptable choice. Large dual-diaphragm condensers are the standard choice for recording vocals, small single-diaphragm condensers are commonly used for distant miking of acoustic ensembles, tiny electrets (lavalieres) are commonly hidden in costumes or in the hairline of actors in theatre and movies, and the even smaller MEMS are commonplace in mobile devices.
Condenser microphones excel in situations where extended high frequency response, fast transient response and a relatively flat frequency response are required. They’re a good choice for almost any acoustic instrument and are commonly used for acoustic guitars, strings, woodwinds and pianos. Although they’re often used as overheads when recording drums, a ribbon is usually a better choice for that application. Similarly, a dynamic or ribbon will often yield a better result than a condenser when close-miking members of the brass family, and when close-miking wooden or metallic percussion that has fast and hard attack transients (e.g. vibraphone, xylophone, etc.).
Traditionally considered as recording tools, condenser microphones have been finding their way on stage with popular music artists in recent years, largely due to developments in handheld condenser mics for vocal use, such as Neumann’s KMS104 and Shure’s Beta 87A or SM86 – although they have always been popular on stage for drum overheads, piano, snare bottom, acoustic guitars and orchestral/chamber music applications.
Indicators: When ribbon mics are too mellow and dynamic mics have insufficient detail, condensers offer the solution. Large diaphragm condensers are a good choice for recording soft sounds due to their high sensitivity and low self-noise. Small diaphragm condensers are a good choice for recording loud sounds due to their lower sensitivity and higher SPL handling. Small single-diaphragm condensers excel at distant miking due to their superior off-axis response and high frequency extension, while large dual-diaphragms are good for close-miking due to their reduced proximity effect and mellower high frequency response.
MAGIC STICKS
The first instalment of this series opened with: “There’s a common misconception among people starting out in audio that the microphone is some kind of magic stick that you point at the sound source and do the rest of the work with knobs, buttons and luck.” Since then we’ve explored ribbon microphones, dynamic microphones and condenser microphones respectively, and looked at the factors that affect their characteristic tonality.
There’s a lot more to microphones than meets the eye and much of it affects the tonality that meets the ear, but none of it is magic. Compared to preamps and converters, the colourations of microphones make them by far the most significant contributor to the tonality of our captured signals. It’s all explained with science and physics, of course, and the only ‘magic’ should be the impression left in the listener’s ear.
Understanding the science and physics of microphones makes it easier to understand how to use them practically. The next instalment in this series looks at microphone specifications – what they mean and how to interpret them. Following that, we transition from the science and physics to the craft of using your ‘magic sticks’ strategically so you don’t have to rely on knobs, buttons and luck to capture a useable sound.